We are Manufacturer, Supplier, Exporter of Hydraulic Bricks Making Machine, Concrete Bricks Making Machines from Satara, Maharashtra, India.
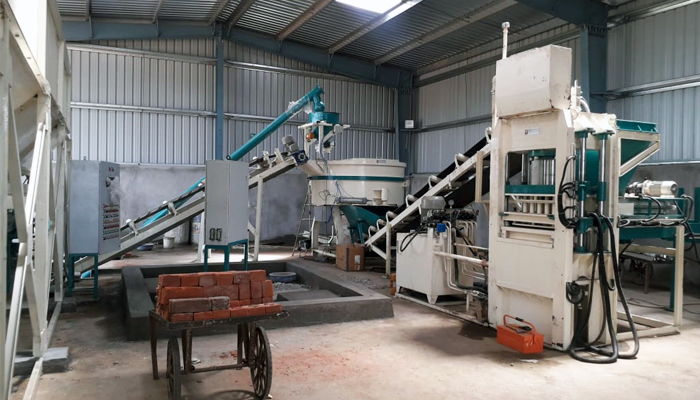
Fly ash bricks are an environmentally friendly alternative to traditional clay bricks. Manufactured using fly ash, a by-product of coal combustion in thermal power plants, these bricks are known for their strength, durability, and energy-efficient production process. They are widely used in building construction due to their low cost, high compressive strength, and eco-friendly nature.
Fly ash brick production gained momentum in the late 20th century, particularly after the environmental push to reduce the carbon footprint of construction materials. The abundant availability of fly ash, which was once considered waste, led to innovations in brick manufacturing, particularly in countries like India, where coal power generation is prevalent. The introduction of fly ash bricks significantly reduced the environmental impact of traditional clay bricks, which require fertile soil and high energy for firing.
The primary purpose of manufacturing fly ash bricks is to provide an eco-friendly and cost-effective alternative to clay bricks, while also utilizing industrial waste in a constructive manner. These bricks offer enhanced durability, reduce energy consumption during production, and contribute to minimizing the need for topsoil, which is extensively used in traditional brick-making.
Fly ash bricks are versatile and can be used in various construction projects, including: